A high-performance engine, gleaming under the fluorescent lights of a workshop, its intricate components meticulously assembled. The first turn of the key brings it to life—a symphony of mechanical precision. But before this powerhouse can unleash its full potential, it must endure a crucial yet often overlooked rite of passage: the break-in period.
The process of breaking in an engine isn’t just about running it for a few miles before hitting the open road. It is an essential phase that determines the engine’s longevity, efficiency, and performance. A poorly broken-in engine may suffer from excessive wear, reduced power output, and premature failure, whereas a properly conditioned one will reward its owner with years of reliability and smooth operation.
The concept of engine break-in dates back to the early days of internal combustion engines when manufacturing tolerances were less precise. In those days, engines required careful conditioning to ensure metal components meshed correctly. Even with modern machining techniques and advanced lubricants, engine break-in remains a vital step in maximizing durability and performance.
The Science of Break-In
Understanding Engine Components
To appreciate the break-in process, it’s important to understand the key components involved:
- Pistons and Rings – The pistons move up and down within the cylinder walls, with rings ensuring proper compression and sealing.
- Cylinders – The smooth inner walls of the cylinders provide the surface against which the piston rings form a seal.
- Bearings and Crankshaft – The bearings support the crankshaft, allowing it to rotate smoothly while minimizing friction.
- Valves and Camshaft – These components regulate the intake of air and fuel and the exhaust of combustion gases, ensuring optimal performance.
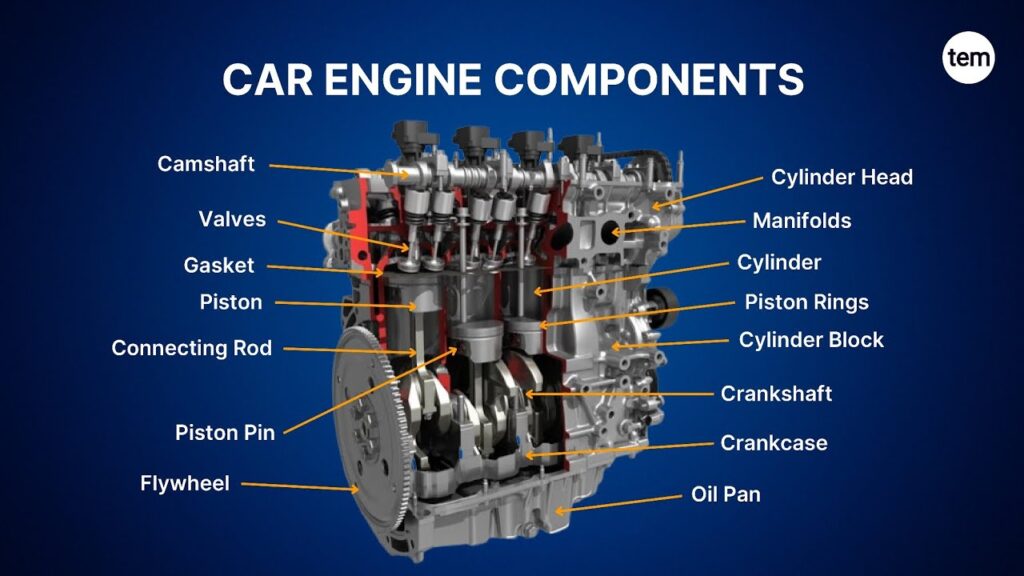
All these components must seat and wear into each other correctly to achieve optimal performance.
The Break-In Process
During break-in, microscopic high points on metal surfaces (known as asperities) wear down gradually. This process allows components like piston rings and cylinder walls to conform perfectly, creating a tighter and more efficient seal.
- Heat and Friction – Controlled friction is necessary to smooth out imperfections, while heat expansion allows components to settle into their final operating state.
- Oil Film Formation – As components move, engine oil plays a crucial role in minimizing wear and preventing excessive friction. Fresh oil must be used during break-in to ensure proper lubrication.
- Carbon Deposits – A well-executed break-in helps prevent excessive carbon buildup, which can degrade performance over time.
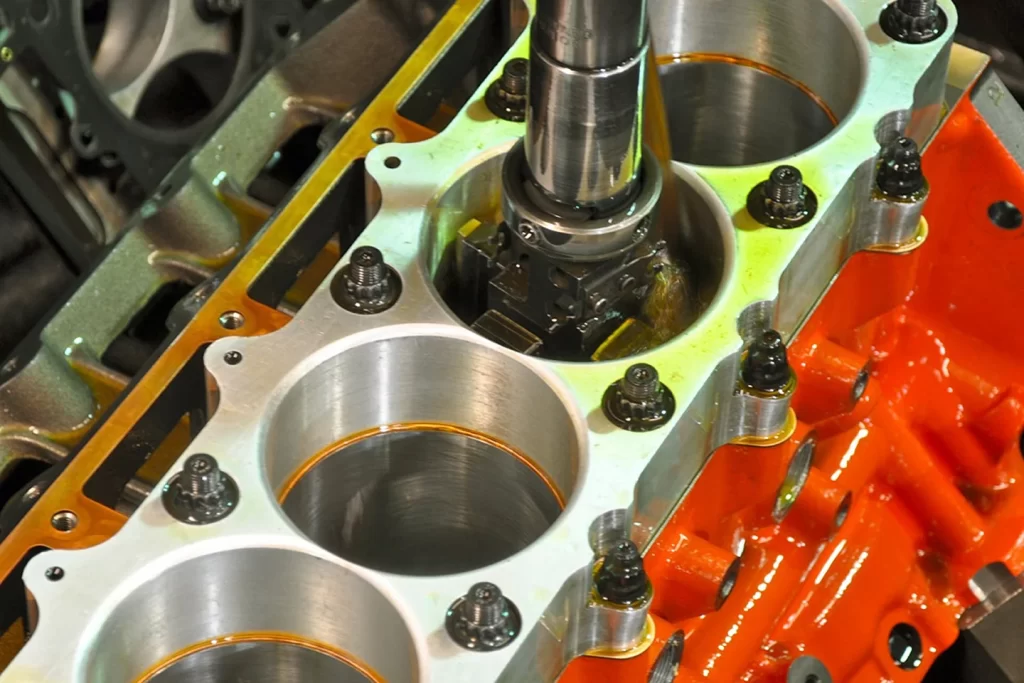
Without a proper break-in, an engine may suffer from poor compression, increased oil consumption, and reduced efficiency.
Break-In Procedures for New Engines
Manufacturer Recommendations
Every engine is designed differently, and automakers provide specific guidelines for the break-in period. Following these recommendations is crucial to ensuring longevity. Common guidelines include:
- Avoid High RPMs – Keeping engine speed moderate (typically below 4,000 RPM) prevents excessive stress on components.
- Vary Engine Load and Speed – Alternating between different speeds and loads helps distribute wear evenly.
- Frequent Oil Changes – The first oil change is particularly important, as it removes tiny metal particles shed during the initial wear-in process.
General Guidelines for a Successful Break-In
In addition to manufacturer recommendations, several universal best practices can enhance the break-in process:
- Avoid Prolonged Idling – Extended idling can prevent proper ring seating and lead to uneven wear.
- No Towing or Heavy Loads – Hauling weight places excessive strain on an engine before it has properly seated its components.
- Steer Clear of Racing or Hard Acceleration – Rapid acceleration and sudden deceleration cause uneven stress and improper wear.
- Maintain Moderate Driving Speeds – Consistent, moderate-speed driving allows all components to adjust evenly.
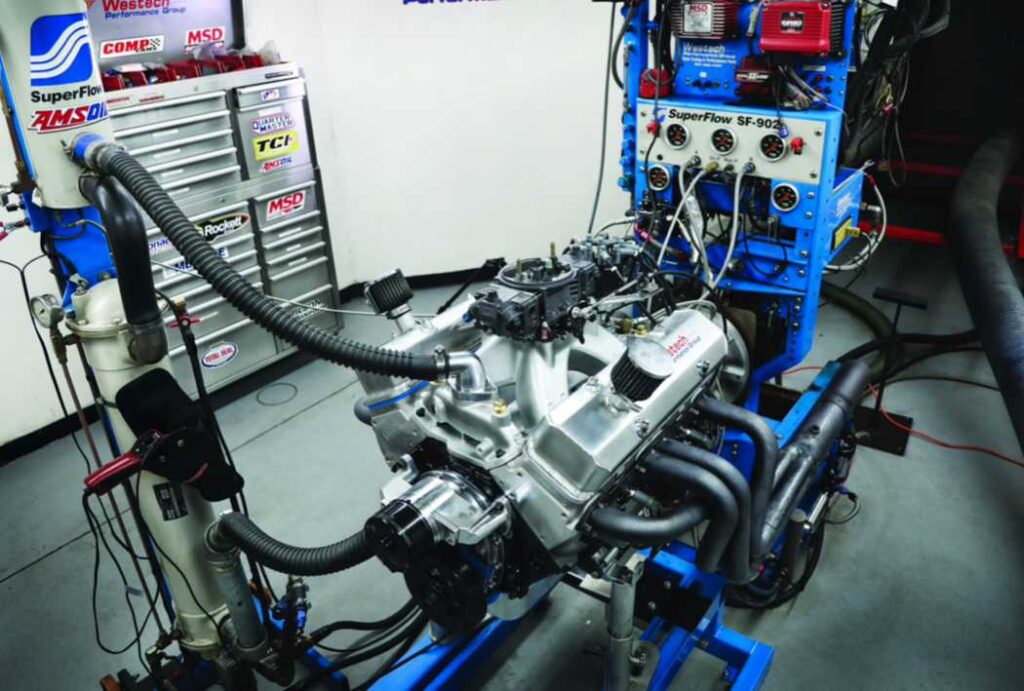
By following these break-in practices, drivers can ensure their engine delivers peak performance and durability for years to come.
Break-In Procedures for Rebuilt Engines
Specialized Considerations
Rebuilding an engine is a meticulous process that restores worn-out components to their original or improved condition. However, the break-in process for a rebuilt engine differs from that of a factory-new engine due to variations in machining tolerances, component replacements, and assembly methods. The extent of the rebuild significantly affects break-in procedures, and understanding these differences is essential for ensuring longevity.
- Top-End Rebuild vs. Complete Overhaul – A top-end rebuild, which primarily involves replacing cylinder heads, valves, and valve seals, may require a shorter break-in process than a complete overhaul, which includes new piston rings, bearings, and crankshaft work.
- Following the Engine Builder’s Recommendations – Unlike mass-produced engines, rebuilt engines often require specialized break-in procedures based on the machining processes and materials used. Engine builders provide tailored instructions that should be followed precisely.
- Frequent Oil Changes – A rebuilt engine may shed more metal particles during the initial break-in period than a new engine, necessitating more frequent oil changes (e.g., after the first 50–100 miles and again at 500 miles). Using high-zinc break-in oil can provide extra protection for flat-tappet camshafts and other critical components.
Neglecting these considerations can compromise the rebuild’s effectiveness and lead to premature wear or failure.
Consequences of Improper Break-In
Premature Engine Wear
Failing to properly break in an engine can have long-term consequences. During the break-in phase, metal surfaces are meant to wear down microscopic high spots and establish smooth, well-seated contact areas. If this process is disrupted, the result can be:
- Scoring and Galling – Inadequate lubrication or excessive heat can cause metal surfaces to wear unevenly, leading to scoring and galling of cylinder walls and bearings.
- Excessive Oil Consumption – Poorly seated piston rings may allow oil to seep into the combustion chamber, resulting in higher oil consumption and smoky exhaust.
- Reduced Engine Life – A poorly broken-in engine may suffer from accelerated wear, leading to costly repairs or early failure.
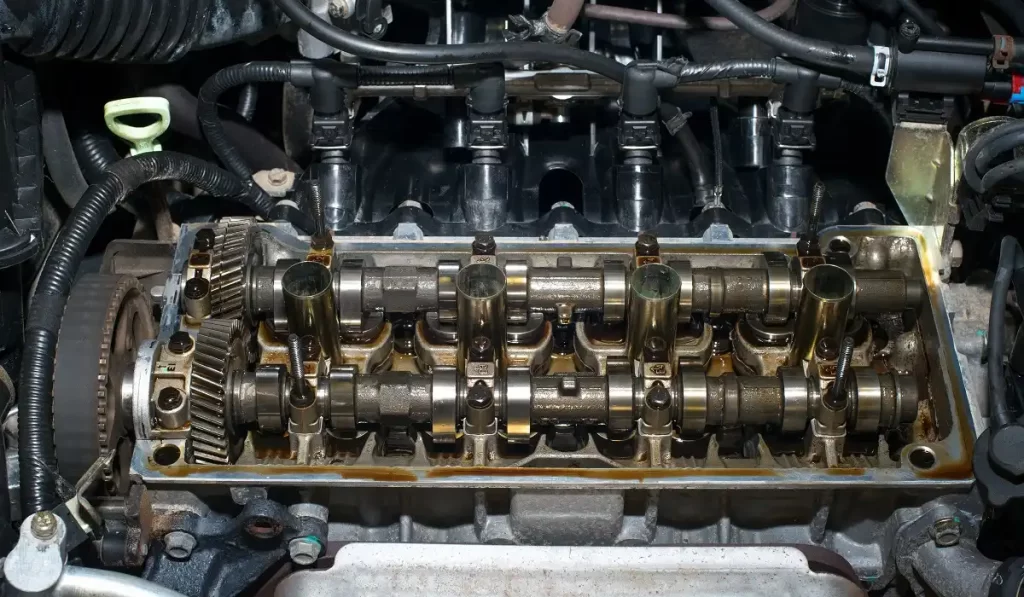
Reduced Performance
An engine that hasn’t been properly broken in may never reach its full potential. Some of the most common performance issues include:
- Lower Power Output – Improper ring seating can result in reduced compression, directly impacting horsepower and torque.
- Increased Fuel Consumption – A rough-running engine with poorly seated components may burn more fuel to compensate for inefficiencies.
- Sluggish Response – Engines that fail to develop proper internal clearances may feel less responsive, making acceleration less sharp and refined.
Reliability Issues
A neglected break-in period doesn’t just impact longevity and performance—it can also lead to unexpected failures. Common reliability concerns include:
- Increased Risk of Engine Knock – Poor ring sealing and uneven wear can contribute to detonation issues, potentially damaging pistons and bearings.
- Overheating – If friction between engine components remains too high due to improper break-in, overheating may occur, leading to potential head gasket failures or warped components.
- Bearing Failure – Insufficient break-in lubrication can cause premature bearing wear, resulting in a loss of oil pressure and catastrophic engine failure.
In short, skipping or mishandling the break-in process can turn a brand-new or rebuilt engine into a ticking time bomb.
Myths and Misconceptions
Despite the wealth of knowledge available today, several myths persist regarding engine break-in procedures. Addressing these misconceptions is crucial for ensuring a successful break-in.
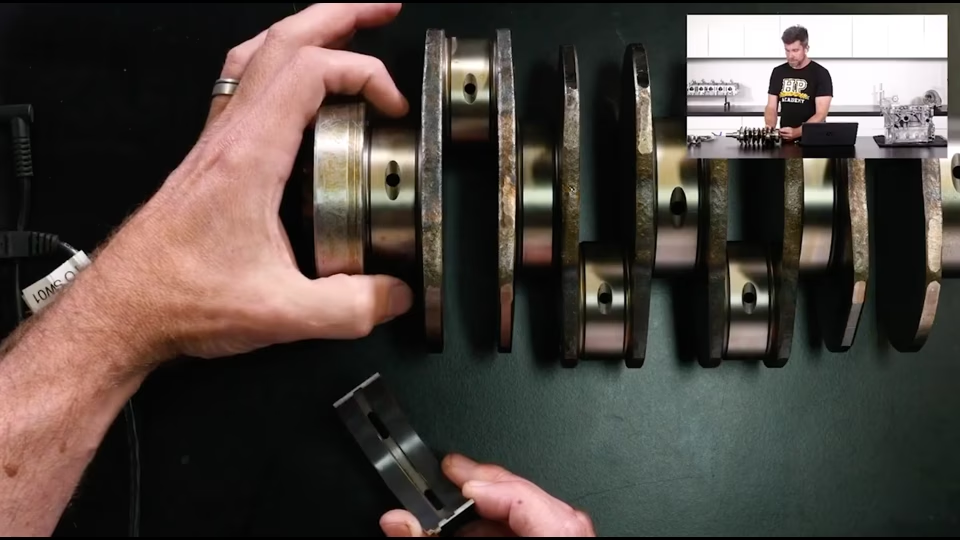
Myth 1: “Hard Break-In” Improves Performance
Some believe that running an engine at high RPMs and under heavy loads right from the start will “seat the rings faster” and improve performance. While controlled bursts of acceleration can help seat piston rings in some high-performance applications, aggressive driving can cause excessive heat, uneven wear, and even permanent damage. A balance between moderate load variation and controlled acceleration is key.
Myth 2: “Breaking in New Oil Is Necessary”
A common misconception is that new oil requires a break-in period before it provides optimal lubrication. In reality, modern lubricants are formulated to provide immediate protection, and using a high-quality break-in oil from the start is more beneficial than “breaking in” the oil itself.
Myth 3: “Sealing the Rings Requires High RPMs”
While it’s true that piston rings need to seat properly against the cylinder walls, the idea that high RPMs are required to “seal” them is misleading. Proper ring seating occurs gradually through controlled operation, and excessive RPMs too early can cause glazing or excessive wear.
Modern engines benefit from advanced machining tolerances, reducing the need for extreme break-in methods. However, best practices still dictate a careful, methodical approach to ensure optimal performance.
Conclusion
Breaking in a new or rebuilt engine is one of the most critical steps in ensuring its longevity, performance, and reliability. Properly seating internal components, managing heat cycles, and following recommended guidelines all contribute to an engine that runs smoothly and efficiently for years to come. Vehicle owners should take the time to read manufacturer or builder recommendations, follow best practices, and prioritize frequent oil changes in the early stages. Cutting corners now can lead to costly repairs and lost performance down the road.
With advancements in engine manufacturing, lubrication technology, and precision machining, the break-in process is evolving. Some modern engines arrive pre-broken-in from the factory, thanks to improved machining tolerances and synthetic lubricants. However, for high-performance, rebuilt, and custom-built engines, a proper break-in procedure remains as crucial as ever.
In the end, patience and attention to detail during those first crucial miles can mean the difference between an engine that lasts a lifetime and one that fails before its time.