When it comes to enhancing vehicle performance and aesthetics, the choice of wheel material plays a pivotal role. Beyond its visual appeal, a wheel’s material can significantly impact factors such as strength, weight, durability, and heat dissipation. In the world of automotive engineering, wheels are produced through three primary manufacturing processes: forging, casting, and flow forming. Each method offers unique benefits and drawbacks, making it crucial for enthusiasts and manufacturers alike to understand their distinctions.
This article explores the intricacies of these manufacturing methods, beginning with the robust and lightweight forged wheels, transitioning to the cost-effective and versatile cast wheels, and culminating in the innovative flow-forming process.
Forged Wheels
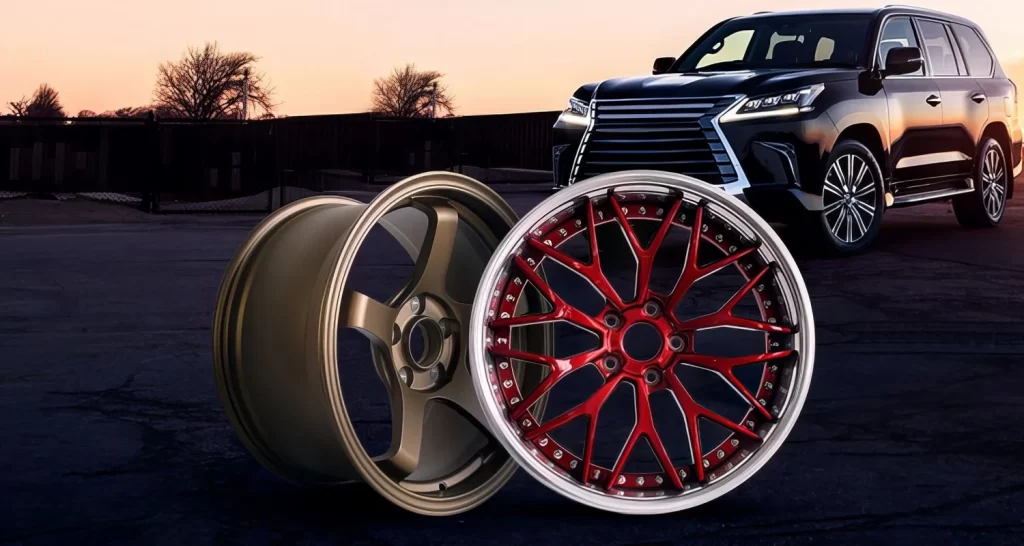
Forging is a manufacturing process that involves shaping metal under extreme pressure using a series of dies. The process starts with a solid block of high-quality aluminum alloy, which is heated and pressed into the desired shape. This compresses the material’s grain structure, aligning it in a way that enhances strength and durability.
Advantages of Forged Wheels
Forged wheels are renowned for their superior properties, which make them a popular choice for high-performance and luxury vehicles.
- Superior Strength and Durability: The forging process results in a dense, uniform material structure, giving the wheels exceptional strength and resilience against stress.
- Reduced Weight for Improved Performance: Forged wheels are significantly lighter than cast wheels of similar dimensions, contributing to reduced unsprung weight. This improves acceleration, braking, and overall handling.
- Enhanced Safety: Thanks to their robust construction, forged wheels are better equipped to withstand impacts and high-stress conditions without cracking or deforming.
- Excellent Heat Dissipation: The dense material allows for efficient heat dissipation, which is particularly beneficial during high-speed driving or braking.
- Customizable Designs and Finishes: Manufacturers can achieve intricate designs and high-end finishes with forged wheels, offering a balance of performance and style.
Disadvantages of Forged Wheels
Despite their advantages, forged wheels come with a few limitations:
- Higher Cost: The forging process involves advanced machinery and labor-intensive techniques, making these wheels more expensive than their cast counterparts.
- Complex Manufacturing Process: The precision and complexity of forging result in longer production times.
Cast Wheels
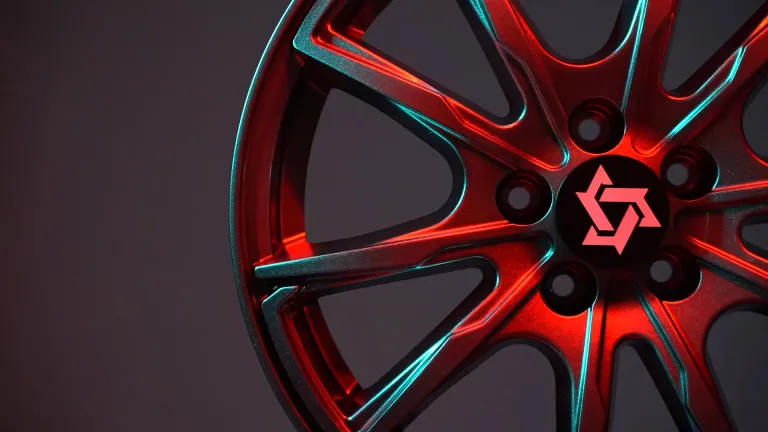
Casting involves pouring molten aluminum alloy into a mold, allowing it to cool and solidify into the desired wheel shape. This process is simpler and more cost-effective than forging, making it a popular choice for mass production. There are several types of casting methods:
- Gravity Casting: Uses gravity to fill the mold with molten aluminum, offering simplicity and cost efficiency but with slightly lower material density.
- Low-Pressure Casting: Utilizes controlled air pressure to force molten aluminum into the mold, resulting in a denser and stronger structure.
- High-Pressure Casting: Provides even higher density but requires specialized equipment and has a higher production cost.
Advantages of Cast Wheels
Cast wheels offer several compelling benefits, particularly for budget-conscious consumers:
- Lower Cost
Casting is a less expensive process, allowing manufacturers to produce wheels at a lower price point without sacrificing too much quality. - Wider Range of Designs and Finishes
The casting process enables the creation of intricate and diverse designs, catering to various consumer preferences. - Faster Production Time
The simplicity of casting allows for quicker turnaround times, making it ideal for large-scale production.
Disadvantages of Cast Wheels
However, cast wheels also have some notable drawbacks:
- Lower Strength and Durability: The grain structure of cast wheels is less uniform, making them more susceptible to cracking or deformation under stress.
- Heavier Weight: Cast wheels are generally heavier than forged wheels, which can negatively impact vehicle performance.
- Less Precision: Variations in the casting process can lead to minor inconsistencies in wheel quality.
Flow-Formed Wheels
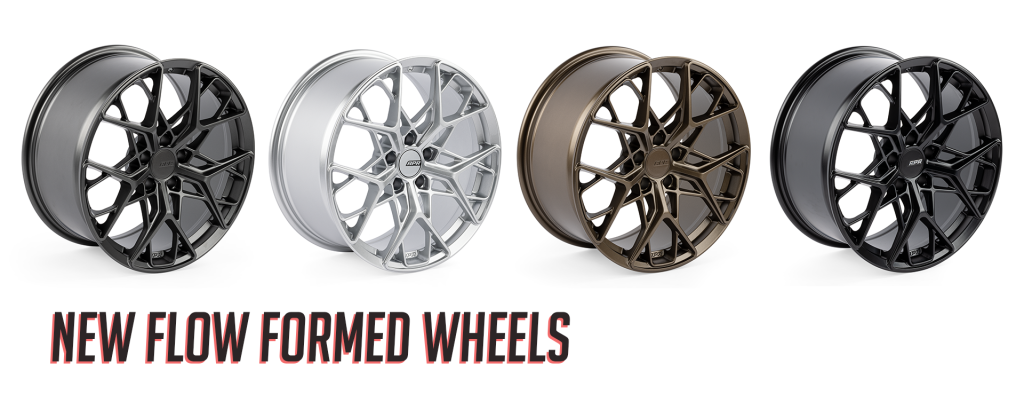
Flow forming is an advanced manufacturing process that blends the benefits of casting and forging. It begins with a cast aluminum wheel blank, which is heated and spun on a mandrel. Rollers are then applied to stretch and compress the wheel into its final shape. This process refines the molecular structure of the aluminum in critical areas, significantly enhancing its strength and durability while retaining cost efficiency.
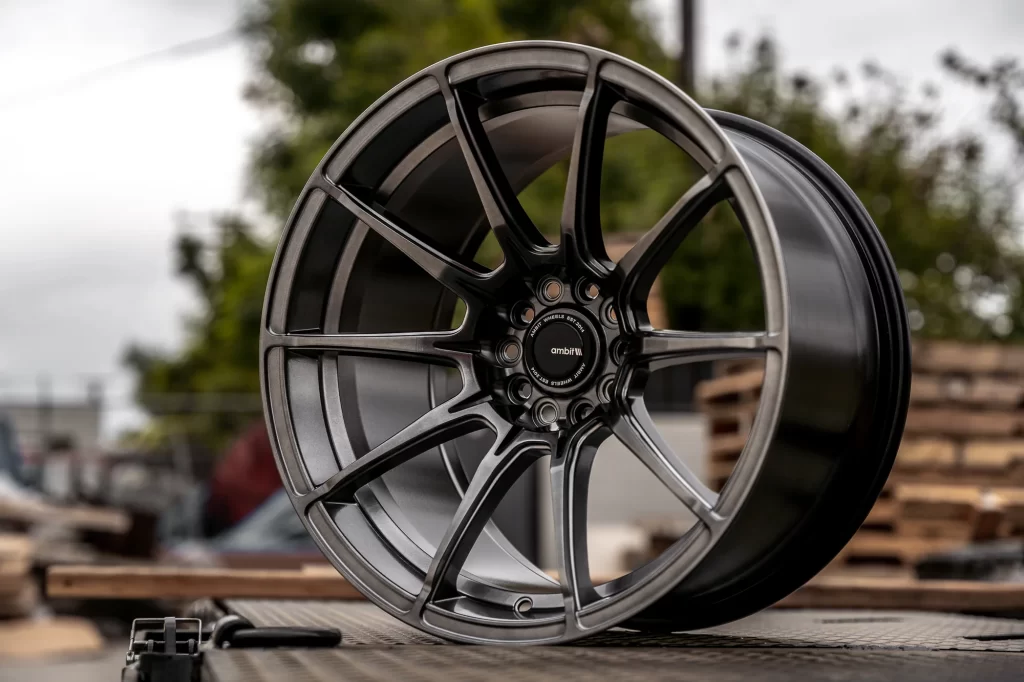
Advantages of Flow-Formed Wheels
- Strong and Durable
Flow-formed wheels exhibit strength levels comparable to forged wheels, thanks to the compression and alignment of the aluminum’s grain structure during the rolling process. - Lighter Weight than Cast Wheels
By reducing excess material and improving structural integrity, flow-forming creates wheels lighter than traditional cast options, improving handling and performance. - Improved Fatigue Resistance
The refined structure of flow-formed wheels increases their resistance to fatigue and wear, making them ideal for long-term use under varying conditions. - Enhanced Heat Dissipation Properties
Like forged wheels, the dense material and precise design of flow-formed wheels allow for effective heat dissipation, which is crucial for performance driving. - Precise Manufacturing Process
The flow-forming process yields highly accurate and consistent results, ensuring uniform quality and structural integrity.
Disadvantages of Flow-Formed Wheels
- Higher Cost than Cast Wheels: While more affordable than fully forged wheels, flow-formed wheels are costlier than standard cast options due to their enhanced properties.
- More Complex Manufacturing Process: The combination of casting and forging techniques requires specialized machinery and expertise, leading to longer production times.
But How To Choose?
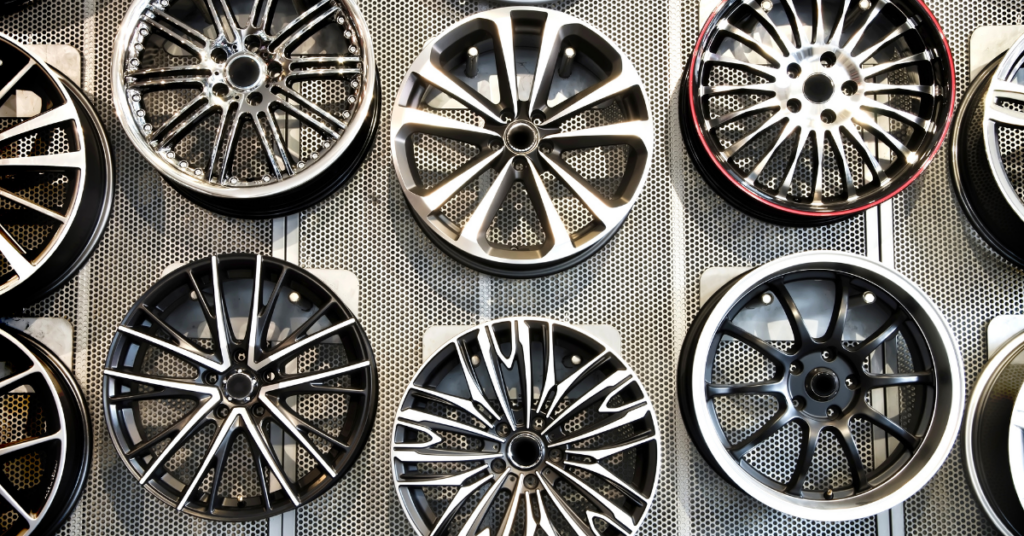
Selecting the right wheel material involves weighing performance needs, budget considerations, and aesthetic preferences. Here’s a framework to guide the decision-making process:
Vehicle Type and Usage
- Daily Drivers: For most everyday vehicles, cast wheels provide a cost-effective solution with a wide range of design options. Their performance is sufficient for typical urban and highway driving.
- Performance Cars: Forged or flow-formed wheels are ideal for performance-oriented vehicles, offering reduced weight, increased strength, and enhanced heat dissipation.
- Off-Road Vehicles: For rugged conditions, forged wheels are recommended due to their ability to endure high stress and impact without deformation.
Budget Constraints
- If affordability is a primary concern, cast wheels are a practical choice.
- For those willing to invest in long-term durability and performance, flow-formed wheels strike a balance between cost and quality.
- Enthusiasts prioritizing top-tier performance should consider forged wheels, despite their higher price.
Desired Performance Characteristics
- Strength: Forged and flow-formed wheels offer superior strength compared to cast wheels.
- Weight: Lighter wheels, such as those produced through forging or flow forming, improve handling and fuel efficiency.
- Aesthetics: Cast wheels often provide a broader variety of designs and finishes, catering to diverse style preferences.
Recommendations
- City Commuters: Cast wheels provide affordability and aesthetic appeal.
- Track Enthusiasts: Forged wheels are the ultimate choice for superior performance under extreme conditions.
- Weekend Warriors: Flow-formed wheels offer an excellent compromise between strength, weight, and cost for occasional spirited driving.
Final Words
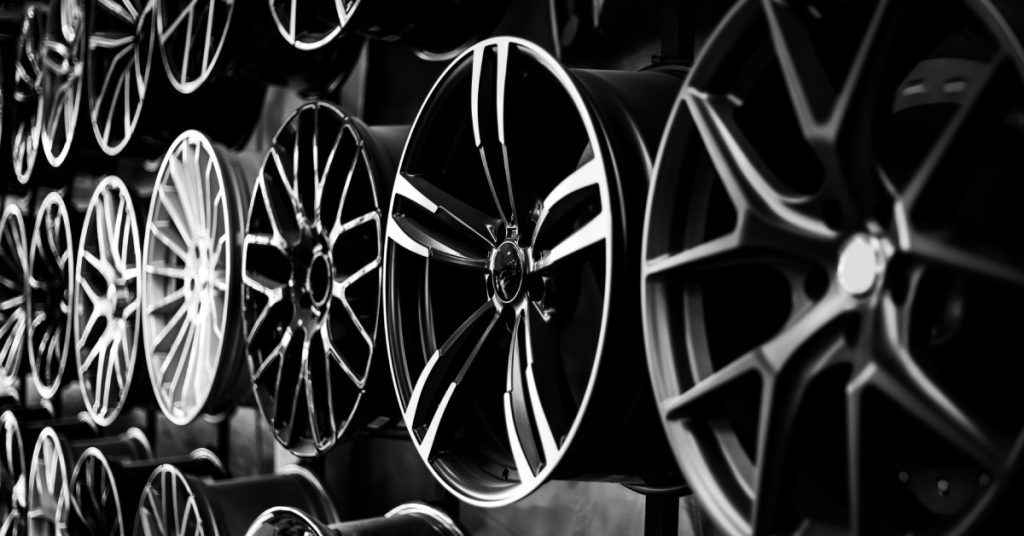
The journey into wheel material technology underscores the importance of selecting the right manufacturing process to align with individual needs. Forged wheels deliver unmatched strength and lightweight performance, cast wheels cater to budget-conscious drivers with diverse designs, and flow-formed wheels blend the best of both worlds.
Choosing the optimal wheel material requires careful consideration of vehicle type, usage, budget, and performance goals. By understanding the distinctions among forging, casting, and flow forming, drivers can make informed decisions that enhance both performance and aesthetics.
For further research, consult automotive experts, explore manufacturer specifications, and consider professional advice to ensure the best choice for your vehicle. Remember, the right wheel material not only elevates performance but also reflects personal style and driving ambitions.